Why Regular Packaging Machine Repair Is Essential for Your Business
Why Regular Packaging Machine Repair Is Essential for Your Business
Blog Article
Quick and Reliable Product Packaging Maker Repair Service Solutions to Reduce Downtime
In the competitive landscape of manufacturing, the performance of product packaging operations depends upon the dependability of equipment. Quick and trusted fixing services are vital in minimizing downtime, which can result in significant operational troubles and monetary losses. Recognizing the value of timely treatments and the role of professional specialists can change how organizations approach repair and maintenance. Nevertheless, navigating the myriad choices readily available for repair service solutions can be challenging. What variables should companies take into consideration to ensure they are making the best selection for their operational requirements?
Value of Timely Services
Prompt fixings of product packaging equipments are crucial for maintaining operational performance and minimizing downtime. In the busy setting of manufacturing and product packaging, also minor malfunctions can result in significant delays and productivity losses. Addressing concerns without delay makes certain that makers run at their ideal capacity, thereby safeguarding the circulation of procedures.
In addition, regular and timely upkeep can stop the rise of minor problems into significant malfunctions, which commonly incur greater fixing expenses and longer downtimes. A proactive approach to equipment repair work not only maintains the stability of the equipment yet likewise enhances the total dependability of the assembly line.
In addition, timely repairs add to the longevity of product packaging machinery. Machines that are serviced immediately are less most likely to experience too much wear and tear, permitting companies to optimize their investments. This is specifically essential in sectors where high-speed packaging is essential, as the requirement for consistent performance is extremely important.
Benefits of Reliable Company
Reputable solution suppliers play an essential duty in making certain the smooth procedure of product packaging machines. Their proficiency not only enhances the efficiency of repair work but additionally contributes considerably to the long life of equipment.
Additionally, a trusted service supplier uses thorough assistance, consisting of training and support for personnel on maker procedure and maintenance finest methods. This not only empowers employees but also grows a society of security and effectiveness within the organization. In general, the benefits of involving trusted company prolong beyond immediate fixings, favorably affecting the entire functional operations of product packaging processes.
Usual Product Packaging Maker Issues
In the world of packaging procedures, various concerns can compromise the performance and functionality of equipments (packaging machine repair). Another usual issue is misalignment, which can create jams and uneven product packaging, impacting product top quality and throughput.
Electrical issues can additionally disrupt product packaging procedures. Defective circuitry or malfunctioning sensors may cause erratic device actions, creating delays and boosted functional costs. Furthermore, software program problems can hinder the maker's shows, leading to operational ineffectiveness.
Irregular item circulation is another vital concern. This can emerge from variations in product dimension, form, or weight, which may affect the device's capability to manage things properly. Not enough training of drivers can aggravate these troubles, as inexperienced employees might not acknowledge very early indications of malfunction or may misuse the equipment.
Dealing with these common product packaging equipment problems promptly is vital to preserving productivity and guaranteeing a smooth operation. Regular examinations and aggressive upkeep can substantially alleviate these issues, fostering a dependable packaging setting.
Tips for Lessening Downtime
To lessen downtime in packaging procedures, applying a positive maintenance website link approach is critical. On a regular basis arranged maintenance checks can recognize prospective issues prior to they intensify, ensuring equipments operate efficiently. Developing a routine that consists of lubrication, calibration, and evaluation of critical parts can considerably reduce the regularity of unexpected malfunctions.
Training team to operate equipment correctly and identify early caution signs of breakdown can also play an essential role. Encouraging operators with the understanding to perform fundamental troubleshooting can prevent minor concerns from look here causing significant hold-ups. Maintaining a well-organized stock of crucial spare parts can accelerate repairs, as waiting for parts can lead to prolonged downtime.
In addition, recording machine performance and upkeep tasks can aid identify patterns and persistent issues, permitting for targeted interventions. Incorporating sophisticated tracking modern technologies can give real-time data, enabling predictive maintenance and reducing the danger of unexpected failings.
Last but not least, cultivating open interaction in between drivers and upkeep groups ensures that any irregularities are promptly reported and dealt with. By taking these aggressive actions, businesses can boost operational effectiveness and substantially minimize downtime in product packaging procedures.
Picking the Right Fixing Solution
Picking the suitable repair work service for packaging machines is a crucial decision that can significantly influence functional effectiveness. A well-chosen you can check here provider ensures that your equipment is fixed quickly, efficiently, and to the highest criteria. Begin by reviewing the supplier's experience with your certain type of packaging tools. A service technician acquainted with your machinery can detect problems more properly and carry out services more quickly.
Next, think about the service supplier's reputation. Looking for feedback from various other businesses within your market can provide insights right into reliability and high quality. Certifications and partnerships with identified equipment makers can also suggest a dedication to excellence.
Furthermore, assess their action time and schedule. A service supplier that can offer timely assistance minimizes downtime and keeps manufacturing circulation steady. It's likewise critical to inquire regarding guarantee and solution guarantees, which can reflect the confidence the supplier has in their job.
Verdict
In conclusion, the relevance of trusted and quick packaging maker fixing services can not be overstated, as they play a vital role in reducing downtime and making sure functional performance. Implementing positive maintenance methods and spending in team training further enhances the longevity of packaging machinery.
Prompt repair services of product packaging machines are essential for preserving operational effectiveness and lessening downtime.Furthermore, prompt repair services add to the long life of product packaging equipment. Generally, the advantages of involving trustworthy solution suppliers expand past instant repair services, favorably affecting the entire operational workflow of product packaging procedures.
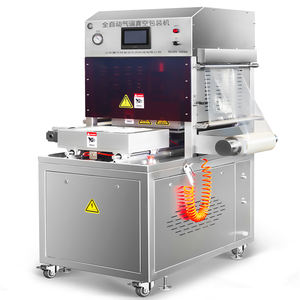
Report this page